Taking care of Ammonia Refrigeration Compressors
Ammonia refrigeration compressors are very efficient and last a long time if cared for. The oil must be able to work for many hours without carrying the ammonia with it or permitting wear. The traditional Naftenic oils are not good at the operating temperatures of these compressors.
The first example is a North American Group II Ammonia Compressor oil with 970 hours of use in a Sabroe compressor at a Coca Cola bottler. It maintained its viscosity without oxidizing and shows little wear.
The rest of the samples are traditional Naftenic refrigeration oils.
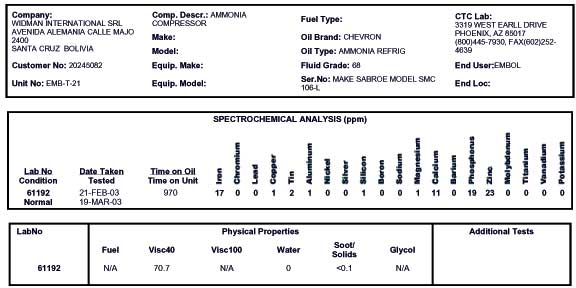
The first problem we encounter is that they did not know how many hours they had used the oil nor how much oil they had added during this time.
The second problem is that the oil is so oxidized that the viscosity increased between 15% and 43%, causing high energy consumption and wear. Iron wear alone was between 84 ppm and 115 ppm.
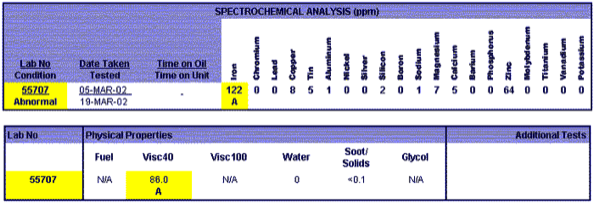
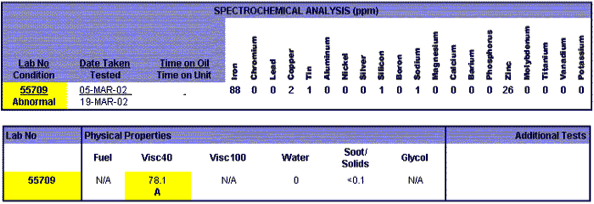
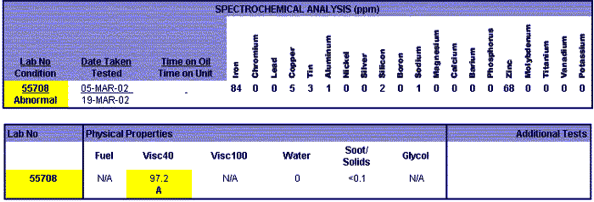
Oxidized oil and the wear it causes
In the next two samples we can see another Naftenic Ammonia compressor oil. This one from one of the biggest oil companies in the world. It has a viscosity index of only 45, so it thickens a lot in the cold part of the compressor and thins out in the hot part.
In the first two examples we can see the problem of oxidation. The viscosity increased between 46% and 60%. Both compressors show high iron wear.
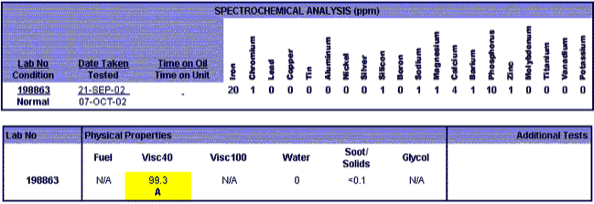
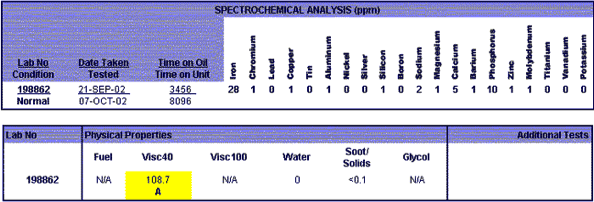
Mixtures of oils when refilling the compressor
This sample shows a serious problem in maintenance. Apparently they used another oil in one of the routine fillings, or used the same re-filling jug they use for hydraulic oil and motor oil. We can see from previous samples that this oil does not contain zinc or phosphorous, but this sample has 120 ppm of detergent from a motor oil and more than 800 ppm of zinc and phosphorous that could be in a motor oil (but the motor oil would have much more calcium).
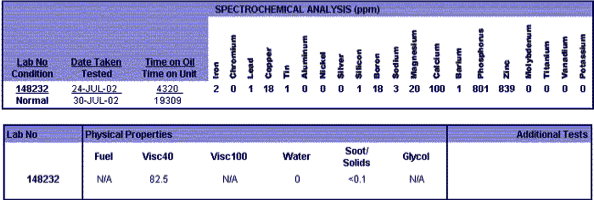
Water can cause severe damage to the compressor
In this first sample we can see the effect of 0.05% water in the compressor oil. It could have been higher at some parts and evaporated, but at the time of the sample it was 0.05%. The rust is 776 ppm.
The second sample shows two problems. In the first result, July 12, we have 943 pp of iron from an increase in viscosity and 0.05% water ingression. It also has Phosphorous from another oil.
In sample 148230 we have 35 ppm of sodium, 716 ppm of Barium (industrial contaminant) and small quantities of zinc and phosphorous.
También podemos ver en la muestra 148230 (la segunda cuadra) que se mezcló otro aceite con el aceite para amoniaco en este compresor.
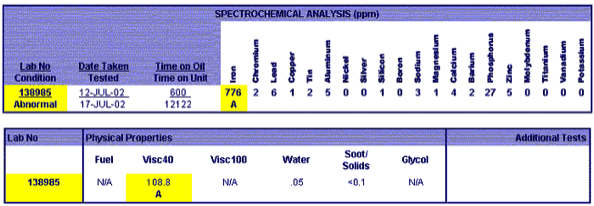
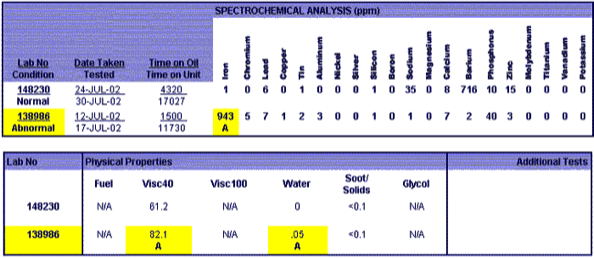

Rust remains after the oil is changed
Even though the oil is changed, if there is not enough anti-rust additive in the new oil, or we don't clean up all of the existing rust, the problems will continue.
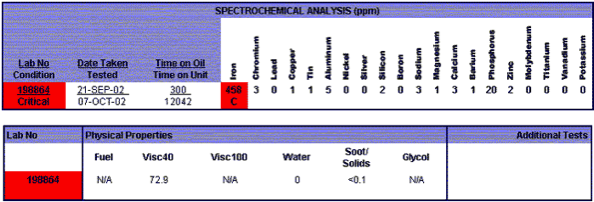
Motor oil should not be put in an Ammonia Compressor
These samples are a naftenic oil from a famous brand. The first compressor has 374 hours on it. It has not been contaminated and does not show high wear, although the 7 ppm of zinc indicates some other oil.
In the second compressor we se an oil with 24 hours of use, and then again 476 hours later, where it is clear that motor oil was added, increasing the Calcium, Zinc and Phosphorous. It is actually running about 30% motor oil. Unless this oil is group II, it will form waxy deposits in the evaporator.
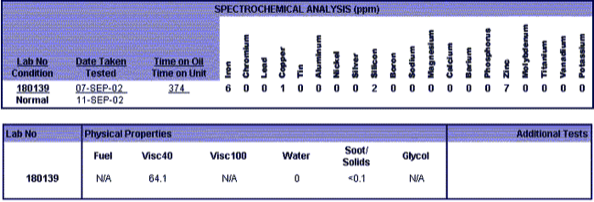
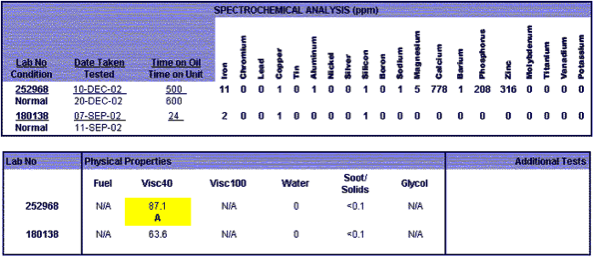