
La Degradación de Lubricantes en la Industria:
Un enemigo silencioso que pone en riesgo sus equipos y su rentabilidad
Por Juan Montiel
Durante años, hemos tenido la oportunidad de trabajar de la mano con ingenieros, técnicos de planta, supervisores y personal de mantenimiento en diferentes industrias, todos responsables de mantener en operación máquinas que deben estar en perfecto funcionamiento y no pueden fallar: turbinas, motores industriales, cajas de engranajes, sistemas hidráulicos, compresores, motores a gasolina/diésel.
Y después de tanto recorrido, de visitas en plantas Alimenticias, Constructoras, Embotelladoras, Ingenios Azucareros, Metalúrgicas, Cementeras, Generación Eléctrica, Empresas Petroleras, Transportistas de alto tonelaje y otras más, cada visita nos ha enseñado algo nuevo, pero siempre nos ha confirmado una realidad de campo que es bastante recurrente:
La degradación del lubricante, un enemigo silencioso que, si no es detectado a tiempo, termina siempre cobrando un alto precio.
Este es el Boletín #242
de nuestro programa de Boletines Informativos mensuales, publicado el primero de mayo, 2025. Todos los boletines están disponibles en formato pdf en https://www.widman.biz
A simple vista, un aceite limpio y sin alteraciones evidentes puede parecer que está en perfecto estado. Sin embargo, en nuestras visitas a plantas hemos comprobado repetidas veces que muchas fallas mecánicas no se originan por desgaste natural, sino por un lubricante que ha perdido sus propiedades mucho antes de que el operador lo imagine o que lo pueda detectar.
El lubricante comienza a degradarse desde el primer momento que sale del envase, cuando entra en contacto con oxígeno. Ese proceso se acelera bajo tres factores que hemos identificado de forma constante:
- Contaminación por agua, partículas o combustibles.
- Temperaturas de operación superiores a las recomendadas por el fabricante.
- Aditivos agotados que no pueden seguir protegiendo superficies de los componentes.
La combinación de estos factores desencadena un fenómeno conocido como oxidación acelerada, lo que incrementa el nivel de acidez, reduce o altera la viscosidad y debilita la película lubricante al punto de colapso. En esa etapa, el aceite deja de ser un protector y se convierte en un catalizador del daño: las partículas metálicas que arrastra terminan multiplicando la velocidad de desgaste de componentes vitales.
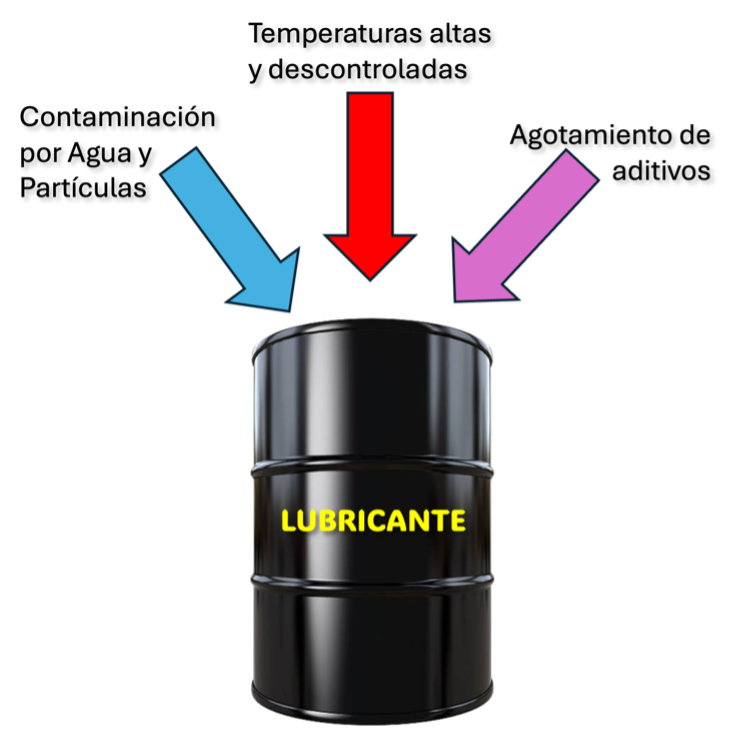
Hemos presenciado esta situación una y otra vez en diferentes industrias y siempre con las mismas consecuencias: fallas mecánicas graves que pudieron evitarse con una detección temprana. A continuación, comparto algunas experiencias:
• Motores diésel industriales:
Analizando aceites que a simple vista lucían en condiciones “normales”, encontramos altos niveles de hierro (Fe), cobre (Cu) y plomo (Pb). En algunos casos, los equipos no mostraban síntomas anormales, pero al abrir motores para inspección o cuando finalmente fallaban, descubríamos cojinetes marcados, cojinetes con barniz, pistones rayados y camisas con desgaste avanzado.
• Sistemas hidráulicos:
Equipos con un diseño de alta precisión que usaban aceites supuestamente correctos, pero que presentaban fallas en válvulas, bombas y cilindros hidráulicos. Los análisis revelaban altos niveles de agua (>1000 ppm), partículas sólidas en niveles ISO 20/19/18 y muy superiores, y en algunos casos presencia de barnices que bloqueaban circuitos internos, casi en la totalidad de las veces el respiradero no habilitado o abierto, pero sin protección, exponiendo al sistema a una contaminación directa. Todo ello sin que el personal de planta hubiera notado nada anormal.
• Engranajes industriales y cajas reductoras:
Las muestras de aceite mostraban una viscosidad alterada, AN (Número Ácido) elevado, y metales de desgaste en concentraciones que indicaban daño activo en los engranajes. A nivel físico, engranajes de bronce color verde-oscuro consecuencia de las reacciones de azufre con la humedad y otros ácidos con la aleación. La realidad era que esos aceites habían perdido hace tiempo sus aditivos antidesgaste y extrema presión, pero seguían en uso porque “el aceite todavía se veía bien” o porque “no había presupuesto para cambiarlo antes del programa.”
• Turbinas y compresores:
Los casos más complejos que hemos atendido han sido en turbinas de generación y compresores de plantas industriales. La formación de barnices y la pérdida de resistencia a la oxidación (indicador RPVOT) derivaron en paradas no planificadas, justo en momentos críticos de operación, generando altos costos operativos e importantes pérdidas en la producción.
Estas experiencias son sólo algunos ejemplos de una realidad que se repite: la degradación ocurre siempre, y en la mayoría de los casos pasa desapercibida hasta que es demasiado tarde.
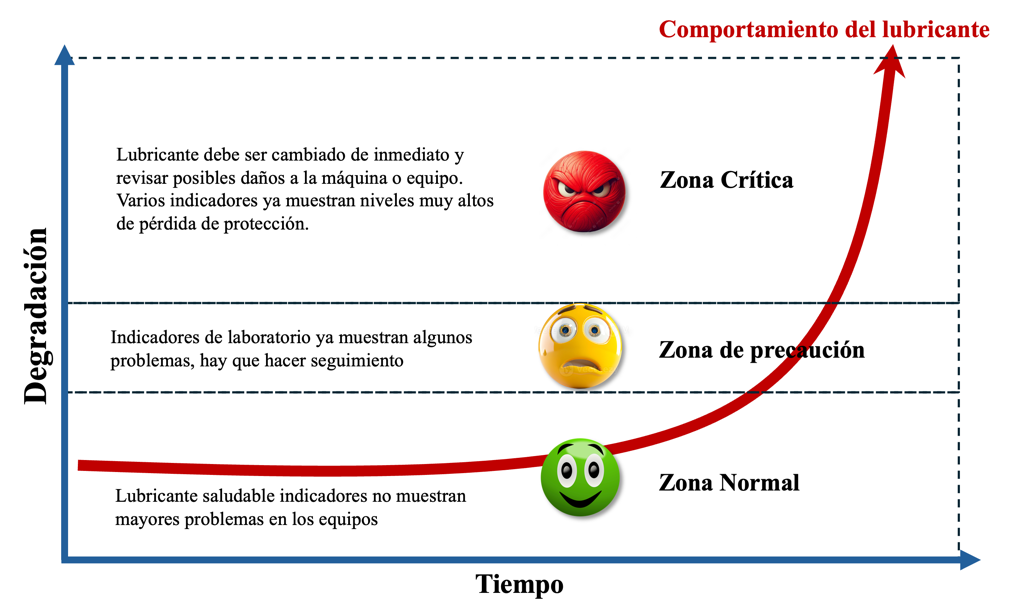
Las consecuencias de no detectar o ignorar la degradación de lubricantes no se hacen esperar. Hemos visto cómo empresas que confiaron en que “el aceite dura lo que promete la etiqueta o la ficha técnica” terminaron pagando reparaciones muy superiores al costo que hubiese tenido un cambio de aceite de buena calidad a tiempo, o un análisis preventivo.
Si a esto se suma el costo de colocar un aceite que no tenga un buen rendimiento o calidad terminamos siempre aplicando la frase: “lo barato cuesta caro”.
Impacto que se puede cuantificar:
- Paradas de producción no planificadas, lucro cesante.
- Daños severos a componentes críticos (rodamientos, ejes, válvulas, engranajes, pistones, cojinetes).
- Aumento acelerado en el consumo de repuestos y mano de obra para mantenimiento correctivo.
- Cambios de aceite prematuros, incrementando el costo de operación y la huella ambiental.
Impacto indirecto para la empresa:
- Pérdida de confiabilidad en la planta.
- Riesgo de incumplimiento de entregas y penalidades contractuales.
- Disminución de la seguridad operativa por fallas de componentes.
- Reducción significativa de la vida útil de activos estratégicos.
¿Cómo identificar que ya está en un problema de degradación?
Para evitar estos escenarios, la detección temprana es fundamental. A lo largo de los años, hemos aprendido que, si un ingeniero o técnico mira los siguientes indicadores, podrá actuar a tiempo y evitar daños mayores:
- AN (Número ácido) elevado: incremento de acidez, oxidación avanzada.
- BN (Número básico) bajo: baja capacidad de neutralizar ácidos.
- Viscosidad alterada: puede ser aumento (oxidación), disminución (dilución por combustible), o contaminación cruzada (mezcla de aceites o viscosidades).
- Presencia de metales: hierro, cobre y plomo en niveles altos son señales de desgaste activo.
- Contaminación con agua o combustible: destruye la película lubricante y acelera la oxidación.
- Presencia de barnices o lodos: visibles en la pieza, por pruebas como MPC o ultrasonido.
- Pérdida de aditivos clave: caídas significativas en calcio, zinc, fósforo, molibdeno, etc. Dependiendo del tipo de aceite.
Aditivos más propensos a degradarse y sus causas
Los aditivos no son eternos, y su degradación o agotamiento es la primera señal de que el aceite está perdiendo su capacidad de protección. A continuación, un resumen basado en nuestras observaciones en campo:
- Detergentes/Dispersantes (Calcio, Magnesio, Sodio): Se consumen al neutralizar ácidos y mantener partículas en suspensión. Se degradan más rápido si hay contaminación con hollín, agua o combustibles de mala calidad.
- Antidesgaste (ZDDP – Zinc y Fósforo): Se consumen en condiciones de alta carga o se evaporan en ambientes de alta temperatura.
- Antioxidantes: Se agotan cuando el aceite se expone a ciclos prolongados de temperaturas elevadas o a la presencia de metales catalizadores de oxidación (hierro, cobre).
- Molibdeno: Se adhiere a superficies desgastadas y se estabiliza en el tiempo, pero en la transición o cuando hay cambios de aceite, sus valores en análisis son fluctuantes.
- Boro: Adherido a las superficies o eliminado por contaminación cruzada. Muy sensible en ambientes con alta presencia de humedad o lodos.
Tabla de elementos más comunes y sus indicadores en laboratorio
Elemento |
ppm |
Comentarios |
Lorem ipsum dolor sit amet, sapien platea morbi dolor lacus nunc, nunc ullamcorper. Felis aliquet egestas vitae, nibh ante quis quis dolor sed mauris. Erat lectus sem ut lobortis, adipiscing ligula eleifend, sodales fringilla mattis dui nullam. Ac massa aliquet. |
|
|
|
|
|
|
|
|
|
|
|
Silicio (Si) |
0 – 10 |
> 10 ppm empieza a mostrar desgaste significativo. Motores nuevos o rectificados pueden tener hasta 2 ppm por encima. |
|
|
|
|
|
|
|
|
|
|
|
|
Hierro (Fe) |
0 – 30 |
Motor pequeño entre 0-10 ppm, motor grande entre 10-30 ppm. |
|
|
|
|
|
|
|
|
|
|
|
|
Cromo (Cr) |
0 – 8 |
Depende mucho de la cantidad de piezas cromadas en el motor. |
|
|
|
|
|
|
|
|
|
|
|
|
Níquel (Ni) |
0 – 2 |
Indica alta contaminación por tierra u Hollín. |
|
|
|
|
|
|
|
|
|
|
|
|
Aluminio (Al) |
0 – 15 |
Depende del diseño del motor. Un bloque de aluminio mostrará más partículas de aluminio y menos de hierro. |
|
|
|
|
|
|
|
|
|
|
|
|
Plata (Ag) |
0 |
Son pocos los motores con cojinetes de Ag. |
|
|
|
|
|
|
|
|
|
|
|
|
Cobre (Cu) |
0 – 10 |
Aceleraciones fuertes o en frío de aceite causarán valores altos. Puede quedar cerca de 5 ppm. Motores con enfriadores pueden tener mas. |
|
|
|
|
|
|
|
|
|
|
|
|
Sodio (Na) |
0 – 10 |
Depende del combustible y medio ambiente. Valores mayores son contaminaciones por agua. A no ser que opere en el salar o cerca del mar |
|
|
|
|
|
|
|
|
|
|
|
|
Plomo (Pb) |
0 – 5 |
Aceleraciones fuertes o largos periodos sin utilizar el motor. Contaminación. Viscosidad del aceite muy baja, o muy alta. |
|
|
|
|
|
|
|
|
|
|
|
|
Estaño (Sn) |
0 – 5 |
Aceleraciones fuertes en algunos motores. Trabajo a bajas revoluciones y alta carga dañando los cojinetes. |
|
|
|
|
|
|
|
|
|
|
|
|
Herramientas prácticas que recomendamos
Para el ingeniero responsable de este tema es muy importante tener herramientas a la mano, muchas veces hemos tropezado con industrias que no otorgan presupuesto o les es difícil entender que deben apartar un presupuesto para estas herramientas, recuerden que en muchas ocasiones el lubricante deja de ser un consumible para convertirse en un activo y como tal debe también debe tener un plan de mantenimiento. Durante nuestras visitas hemos comprobado que las plantas más exitosas aplican sistemáticamente:
- Análisis de lubricante usado: permite conocer el estado real del aceite y la condición interna de la máquina.
- Monitoreo de tendencias: no basta con un valor aislado. Hay que interpretar la evolución en el tiempo y las condiciones como km recorridos u horas trabajadas, así se hacen comparaciones útiles.
- Filtración eficiente y control de contaminación, secado y protección: prolonga la vida útil del lubricante.
- Capacitación del personal: para que entiendan la importancia de cada parámetro y puedan actuar con anticipación.
- Soporte profesional: La mayor parte de las veces dentro la empresa debemos escuchar a expertos opinar sobre la forma que hacemos mantenimiento para recolectar últimas tecnologías y nuevos procesos para mejorar el trabajo. En el caso de Widman International tenemos una plantilla de profesionales trabajando en campo y de manera virtual para ayudar a las industrias.
Tabla de referencia para detectar degradación del lubricante con algunos indicadores guía
Indicador |
Qué mide |
Límite |
Límite |
Aplicación |
Posibles Causas |
|
|
|
|
|
|
|
|
|
Viscosidad (40°C o 100°C) |
Cambio en resistencia al flujo |
±10% del valor original |
±15% del valor original |
Todos |
Oxidación, contaminación con combustible o agua, mezcla de aceites |
|
|
|
|
|
|
|
|
|
AN (Número de Ácido) |
Formación de ácidos por oxidación |
+0.03 +0.5 mg KOH/g |
0.5 +1.0 mg KOH/g |
Turbinas, compresores. Hidráulicos, reductores |
Oxidación avanzada, alta temperatura, ingreso de aire |
|
|
|
|
|
|
|
|
|
BN (Número Básico) |
Capacidad para neutralizar ácidos |
- 40% del valor nuevo |
≤4 |
Motores |
Degradación de aditivos, operación prolongada, entrada de contaminantes ácidos |
|
|
|
|
|
|
|
|
|
Contenido de Agua (KFischer) |
Contaminación con agua (ppm o %) |
> 300 ppm > 750 ppm |
> 500 ppm > 1000 ppm |
Hidráulicos, turbinas, compresores engranajes |
Condensación, fugas en intercambiadores, lavado incorrecto |
|
|
|
|
|
|
|
|
|
Oxidación (FTIR) |
Productos resultantes del envejecimiento del aceite |
> 5 Abs/cm > 7 Abs/cm |
> 7 Abs/cm > 10 Abs/cm |
Hidráulico, turbinas, compresores Engranajes |
Alta temperatura, operación prolongada, bajo RPVOT |
|
|
|
|
|
|
|
|
|
Nitración (FTIR) |
Ingreso de gases de combustión (óxidos de nitrógeno) |
> 15 Abs/cm |
> 20 Abs/cm |
Motores, compresores |
Inyección pobre, baja combustión, entradas de gases al cárter |
|
|
|
|
|
|
|
|
|
Metales de desgaste (Fe, Cu, Pb) |
Presencia de desgaste metálico interno |
Fe > 100 ppm / Cu > 10 ppm |
Fe > 300 ppm / Cu > 80 ppm |
Motores, engranajes, compresores |
Alineación incorrecta, baja lubricación, contaminación por partículas |
|
|
|
|
|
|
|
|
|
Combustible diluido (%) |
Contaminación por diésel o gasolina en el aceite |
> 1 % |
> 2.5 % |
Motores |
Inyectores defectuosos, arranque frecuente en frío, bypass de anillos |
|
|
|
|
|
|
|
|
|
Hollín o Carbonilla (%) |
Presencia de residuos sólidos de combustión |
> 1% |
> 2% |
Motores diésel |
Filtros de aire sucios, mala combustión, uso prolongado de aceite |
|
|
|
|
|
|
|
|
|
ISO 4406 |
Nivel de contaminación por partículas sólidas |
> 18/16/13 |
> 20/18/15 |
Hidráulicos, turbinas |
Fugas, sellos defectuosos, mal filtrado, apertura del sistema |
|
|
|
|
|
|
|
|
|
Espuma (Sec. I/II/III) |
Formación y persistencia de burbujas |
> 50 ml |
> 150 ml |
Hidráulicos, engranajes |
Contaminación por agua, detergente incorrecto, agitación intensa |
|
|
|
|
|
|
|
|
|
Demulsibilidad |
Tiempo que tarda en separar el agua |
> 20 min > 15 min |
> 30 min > 20 min |
Hidráulicos, engranajes. Turbinas, compresores |
Degradación química, ingreso de contaminantes polares, mezcla con otros aceites |
|
|
|
|
|
|
|
|
|
Depleción de aditivos (%) |
Consumo de antioxidantes, AW, EP, etc. |
- 15% |
-30% |
Todos |
Alta temperatura, oxidación, filtración excesiva |
|
|
|
|
|
|
|
|
|
Ferrografía (analítica) |
Forma y severidad de partículas metálicas |
Moderado |
Corte, fatiga o abrasión severa |
Motores, engranajes, turbinas |
Fallas de contacto, lubricación deficiente, sobrecarga |
|
|
|
|
|
|
|
|
|
RPVOT |
Capacidad antioxidante residual del lubricante |
< 50% del valor nuevo |
< 25% del valor nuevo |
Turbinas, hidráulicos |
Agotamiento de antioxidantes, oxidación acelerada |
|
|
|
|
|
|
|
|
|
MPC |
Tendencia del aceite a formar barnices (colorimetría) |
> 15 |
> 30 |
Turbinas, compresores, hidráulicos |
Alta temperatura localizada, oxidación térmica, baja circulación |
|
|
|
|
|
|
|
|
|
FTIR - Aditivos específicos |
Presencia o reducción de componentes como AW, EP, detergentes |
Pérdida > 15% |
Pérdida > 30% |
Motores, engranajes |
Contaminación, oxidación, mezclas incompatibles |
|
|
|
|
|
|
|
|
|
Ultrasonido en aceite |
Presencia de aire, cavitación, formación de burbujas |
Niveles altos anormales |
Pico sostenido constante |
Hidráulicos, compresores |
Aire atrapado, cavitación en bombas, fugas internas |
|
|
|
|
|
|
|
|
|
Tabla de referencia de degradación por Tipo de Lubricante
Tipo de Lubricante |
Indicadores Clave |
Precaución |
Crítico |
Causas más comunes |
|
|
|
|
|
|
|
|
|
|
Hidráulico |
RPVOT, ISO 4406, Agua, Espuma, MPC |
RPVOT < 70%, ISO > 18/16/13, Agua > 500 ppm |
RPVOT < 50%, ISO > 20/18/15, MPC > 30, agua>1000ppm |
Fugas, humedad ambiental, sellos deteriorados, filtros saturados |
|
|
|
|
|
|
|
|
|
|
Turbina |
RPVOT, MPC, AN, FTIR Oxidación |
RPVOT < 70%, AN > 1.0, MPC > 15 |
RPVOT < 50%, AN > 2.0, MPC > 30 |
Alta temperatura, agua condensada, largas horas de operación continua |
|
|
|
|
|
|
|
|
|
|
Compresor |
MPC, FTIR, AN, Metales |
Oxidación > 20 Abs, MPC > 15 |
MPC > 30, AN > 2.0, Fe > 200 ppm |
Fallas en el sello, temperatura elevada, bypass del gas |
|
|
|
|
|
|
|
|
|
|
Engranajes industriales |
Ferrografía, ISO, FTIR Aditivos |
Fe > 150 ppm, aditivos < 70%, ISO > 18/16/13 |
Corte severo en ferrografía, aditivos < 50% |
Sobrepresión, carga intermitente, lubricación incorrecta, contaminación con polvo |
|
|
|
|
|
|
|
|
|
|
Motores (diésel/gasolina) |
BN, Hollín, Metales, Combustible, FTIR |
BN < 50%, hollín > 2%, combustible > 1.5% |
BN < 25%, hollín > 4%, combustible > 3%, Fe > 300 ppm |
Inyectores desgastados, mala combustión, intervalos de cambio extendidos |
|
|
|
|
|
|
|
|
|
|
Soluciones
En Widman Internacional siempre exigimos que los productos que se apliquen sean los de mejor calidad por su rendimiento y no por precio, preferimos ver resultados positivos y protección para sus activos de las empresas, por eso recomendamos:
- Seleccionar y utilizar aceites de base Grupo II o más altos con formulaciones que resistan más tiempo la oxidación y la degradación.
- Implementar programas regulares de análisis de aceite usado, bajo un plan y toma de muestra (Boletín 156).
- Utilizar técnicas de filtración, secado, protección y buenas prácticas de almacenamiento.
- Tener protocolos claros de acción cuando los indicadores superen los límites de precaución.
- Capacitar al personal para poder entender las implicaciones que tiene el no controlar la degradación del lubricante.
- Crear su propia tabla de indicadores de referencia que estén adecuados a su empresa, así puede tener un programa de mejora continua.
- Consultar con especialistas o expertos cada vez que el laboratorio entregue un reporte que se aparte de los rangos normales.
Conclusión
Nuestra experiencia en Widman International nos enseña que el lubricante no es simplemente un gasto operativo, sino la primera línea de defensa contra el desgaste prematuro y las fallas catastróficas, por lo que observar su degradación, ayudará a mantener el activo de la empresa.
Invertir en lubricantes de calidad, en análisis y monitoreo y en buenas prácticas operativas es la diferencia entre tener equipos trabajando con fiabilidad por años o sufrir costosas reparaciones imprevistas.
No espere a que su equipo “suene raro” o “suba temperatura” o “se descontrole” para actuar. La degradación avanza sin aviso y los costos de no detectarla a tiempo son mucho mayores que los de prevenirla.
Desde Widman International, seguimos comprometidos en acompañar a cada uno de ustedes no solo en la venta de lubricantes, sino en construir sistemas de mantenimiento más inteligentes y rentables.
La información de este boletín técnico es de única y completa propiedad de Widman International S.R.L. Su reproducción solo será permitida a través de una solicitud a info@widman.biz no permitiendo que esta altere sus características ni su totalidad.
Visitantes a este sitio